Pre/Post-Bunkering Analysis
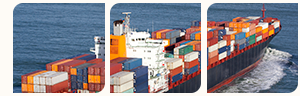
Pre-Bunkering Routine Analysis
The challenge
- Short turnaround time is the main challenge. To avoid the off-specification fuel on board a vessel to reduces the risk of costly engine damage and expensive debunkering. A pre-bunker analysis provides an independent assessment on the quality of the fuel on the barge before it arrives at the vessel.
How it works
- A pre-bunker analysis involves collecting representative samples from the barge tanks and testing them. The aim of a pre-bunker analysis is to have the completed analysis before the barge delivers to the vessel. This will enable the ship-owner or manager to make an informed decision whether or not to accept the bunkers before they are supplied.
Key benefits
- 24 hours turnaround time, regardless of what testing or assessment of fuel quality before bunkers are delivered.
- Prevention of the delivery of a poor quality fuel on-board.
- Local facilities in key ports allowing fast turnaround of analysis.
- Eurofins personnel remain in contact with the fuel supplier to avoid or minimize potential delays.
- Samples are transported to bunker fuel lab, where a volumetric composite of all tanks sampled is prepared.
- Composite samples are tested by Eurofins to selected modified test methods for screening of problematic 2020 fuels.
- Testing is prompt, between 6-12 hours. If fuel parameters fail to meet the fuel specification, additional testing and time may be required.
- Results are reported to the vessel and/or client before the barge commences pumping bunker fuel to the vessel, so that the fuel quality designated for that client vessel is confirmed and known prior to bunkering.
- In most cases, barges are instructed by the supplier to wait for Eurofins results before fuel pumping operations.
- Sampling of the barge is a critical part of the operation, as non-representative samples affect quality. The Eurofins surveyor is instructed to follow proper sampling procedures. Copies of the sampling procedure and pre-testing analysis protocol are included with client quotations.
Chemical Nature of fuels
- Compatibility / Stability assessment by Spot Test
- Asphaltene
- Xylene Equivalence
- Toluene Equivalence
- Toluene Insolubles
- Chemical contaminants analysis by GCMS – ASMT D7845
Bunker Chemical Contaminants Analysis (ASTM D7845 - international standard)
- Ethylbenzene-d10 (CAS. No: 25837-05-2)
- n-butyl alcohol (CAS. No: 71-36-3)
- Cyclohexanol (CAS. No: 108-93-0)
- n-butyl ether (CAS. No: 142-96-1)
- n-butyl acrylate (CAS. No: 141-32-2)
- Styrene (CAS. No: 100-42-5)
- alpha-pinene (CAS. No: 80-56-8)
- Phenol (CAS. No: 108-95-2)
- alpha-methyl styrene (CAS. No: 98-83-9)
- beta-pinene (CAS. No: 19902-08-0)
- 4-methyl styrene (CAS. No: 622-97-9)
- trans-B-methyl styrene (CAS. No: 873-66-5)
- 3-methyl styrene (CAS. No: 100-80-1)
- 2-methyl styrene (CAS. No: 611-15-4)
- Dicyclopentadiene (DCPD) (CAS. No: 77-73-6)
- Limonene (CAS. No: 5989-27-5)
- Indene (CAS. No: 95-13-6)
- 1-phenyl ethanol (CAS. No: 98-85-1)
- para, alpha-Dimethyl styrene (CAS. No: 1195-32-0)
- 2,5 dimethyl styrene (CAS. No: 2039-89-6)
- 2,4 dimethyl styrene (CAS. No: 2234-20-0)
- 2-phenyl ethanol (phenylethanol) (CAS. No: 60-12-8)
- 2-Ethyl Phenol (CAS. No: 90-00-6)
- 2,4 Dimethyl Phenol (CAS. No: 105-67-9)
- 4-Ethyl Phenol (co elutes with 3-ethylphenol) (CAS. No: 123-07-9) (CAS. No: 620-17-7)
- 2-Phenoxy-1-propanol (CAS. No: 4169-04-4)
- 2-Phenoxy ethanol (CAS. No: 122-99-6)
- 4-isopropylphenol (CAS. No: 99-89-8)
- 1-Phenoxy-2-Propanol (CAS. No: 770-35-4)
- Styrene Glycol (CAS. No: 93-56-1)
Other Contaminants and Properties
- Kinematic velocity @40,50 & 100°C
- Density @ 15°C
- Sulphur
- Flash point
- Hydrogen sulphide
- Total acid number/ Strong acid number
- Total sediment accelerated/potential/existent
- Sediment by extraction
- Micro Carbon Residue (MCR)
- MCR (10% distillation bottoms)
- Water by distillation
- Ash
- Pour point
- Aluminium & Silicon
- Vanadium
- Sodium
- Calcium, Zinc & Phosphorus
- Heat of combustion (CGV or NCV)
- Calculated Carbon Aromaticity Index (CCAI)
- Distillation of petroleum products
- Cetane index
- Cloud point
- Cold Filter Plugging Point (CFPP)
- Cleanliness & compatibility
- Lubricity
- Oxidation stability
- Aspheltane
- Nitrogen content
- Wax content
- Total base number
- Pentane/ Toluene insolubles
- ASTM colour
Screening
- FAME, Fatty Acid by FTIR/GCMS
- Aromatic or Chlorinated Solvent by Head Space/ GCMS
- DCPD/ Styrene by GCMS
- Polymers (Polyethylene, Polypropylene, Polystyrene) by FTIR
Microbiological Aspects (IP385)
- Cladosorium Resinae (estimated)
- Penicillium (estimated)
- Yeast
- Total colony count
- others...
Oil Spill Dispersants
- Dispersant capacity
- Flash point
- Biodegradability
- Chlorinated hydrocarbons
- Aromatic hydrocarbons
- Toxicity
Post-Bunkering Routine Analysis
- As well as comparing Fuel Quality Testing results against client’s fuel purchasing specification, fuel quality checks can also be made for compliance with IMO and EU regulatory requirements.
- Eurofins introduced the concept of fuel quality testing bunker purchases in at a time when deteriorating bunker quality and escalating fuel prices were giving ship operators massive problems. Today, bunker quality has not improved and must be continuously monitored to ensure it meets specifications. Due to increased secondary refining, blending activities as well as potential contamination from sources within the supply chain. In addition, stricter environmental regulations and the introduction of more Emission Control Areas (ECA) have necessitated increased use of low sulphur fuels and also distillates which are not without fuel quality issues.